
On the other hand, ERP system collaborates all such operations onto a single platform. Also, collaborating with different departments or team members for a common issue or task becomes difficult.
#Act by sage look up customers by age software
Using separate software for individual operations leave a room for errors and result in disparate information. Think of a company running multiple operations – finance, accounting, human resource management, IT infrastructure, inventories and multi-language/ currencies.
#Act by sage look up customers by age full
What is ERP? The easiest way to define ERP is understanding its full form – Enterprise Resource Planning. The Enterprise Resource Planning market is growing at an approximate of 15% annually and is expected to reach $85.9 billion by 2022. These are the business intelligent software systems that come with advanced reporting, predictive analysis, customer service, and sales and marketing automation features.

Modern ERP software manages supply chain, finance and accounting along with other company operations. Along with web access, they run smoothly both on mobile and from remote locations. They are usually cloud-based and are being delivered through SaaS model. Today’s Enterprise Resource Planning systems have evolved even more. This ERP was capable of integrating different software used by companies onto a single platform. Towards 2000s, there were substantial developments in the software and it was being deployed over the internet. In early 1990, Gartner Group coined the software term – Enterprise Resource Planning explaining it to be an extended version of MRP and MRP II.Įnterprise Resource Planning included back office functionalities like project management, HR, accounting and finance, and engineering. In 1980s, the MRP optimized its performance with added features around capacity requirements and was termed as MRP II. In addition to this, financial management software were being developed too, but as a separate entity.
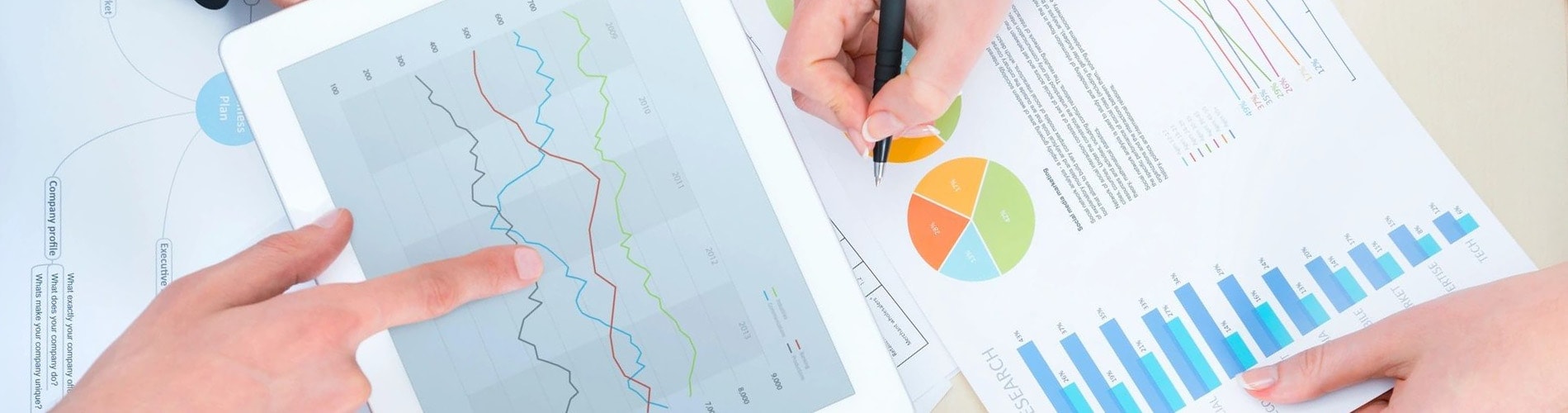
Later in 1972, a German company created real-time business software, which was a completely new concept altogether back then. The software was running on mainframe computers with average computing skills as compared to present day laptops. By 1975, majority of the firms were using MRP software to manage their manufacturing process, however, the cost incurred was manageable only by large sized companies. This helped companies to utilize their resources better. Companies were benefitted in terms of stocking up the required inventory only, instead of investing heavily at once. Materials Requirement Planning (MRP) software was created to plan the entire manufacturing process from production to delivery. With the birth of cloud computing in 1960s, factory production raised, which created a need to manage production striking the right balance along with maintaining customer demands.
